Dans des articles précédents, nous avons discuté des techniques de revêtement de poudre sur métal et du processus de revêtement de poudre d’aluminium. Dans cet article, nous nous concentrons sur le revêtement chimique par film en tant que protection de surface métallique importante et un processus de prétraitement efficace pour la peinture et le revêtement en poudre.
L’article met en évidence certains des métaux sur lesquels vous pouvez utiliser un revêtement chimique par film et les différents types de revêtements de conversion que vous pouvez envisager.
De plus, nous abordons les avantages et inconvénients du revêtement chimique par film, les processus impliqués et les applications industrielles.
Enfin, nous vous guidons à travers les processus de maintenance et de réparation des finitions de revêtements chimiques par film les plus courantes.
Mais d’abord, la définition
1. Qu’est-ce que le Revêtement Chimique par Film ?
Le revêtement chimique par film ou le revêtement de conversion chimique fait référence à un processus chimique ou électrochimique permettant de transformer la surface métallique de votre composant en une couche résistante à la corrosion.
La couche protectrice formée chimiquement peut se présenter sous forme de composés de phosphate ou d’oxydes.
Le revêtement chimique par film est couramment utilisé pour la passivation de l’aluminium et de ses alliages. Cependant, vous pouvez également le considérer pour d’autres métaux tels que cuivre, zinc, titane, magnésium, acier, argent et cadmium.
Outre la création d’une couche résistante à la corrosion, le revêtement chimique par film laisse votre surface métallique parfaitement prête pour des options de peinture ou de revêtement en poudre.
2. Comment Appliquer des Revêtements Chimiques par Film sur les Pièces Métalliques
Voici quelques-unes des techniques que vous pouvez adopter pour appliquer une solution de revêtement chimique par film appropriée à votre pièce métallique :
2.1. Revêtement Chimique par Film – Méthode d’Immersion
Le processus d’immersion consiste à immerger votre pièce ou composant métallique dans une solution chimique. Vous avez besoin d’un réservoir spécial pour cela.
La réaction entre la solution chimique et votre pièce métallique forme une couche mince de protection contre la corrosion et d’autres éléments environnementaux agressifs.
Pour que la couche chimique formée adhère à votre surface métallique, la solution chimique est agitée par de l’air.
Après avoir atteint l’épaisseur de revêtement désirée, vous retirez simplement la pièce de la solution après environ 5 minutes pour la rinçage, le séchage et le durcissement.
2.2. Revêtement Chimique par Film – Méthode de Pulvérisation
Cela implique de pulvériser vos pièces métalliques dans une zone fermée spéciale à l’aide d’une solution chimique contenant des chromates ou d’autres solutions chimiques adaptées.
La solution pulvérisée réagit avec la surface de votre pièce métallique pour former une couche protectrice et résistante à la corrosion.
Vous rincez ensuite et séchez votre composant, prêt pour un revêtement secondaire ou à utiliser tel quel sans autre revêtement.
2.3. Chem Film – Méthode du Brossage
En utilisant une brosse douce appropriée, vous appliquez une solution chimique contenant des chromates ou d’autres solutions adaptées sur vos pièces fabriquées.
Tout comme lors de la pulvérisation, la solution pulvérisée forme une couche protectrice sur vos composants. Le processus est terminé en rinçant et séchant complètement vos pièces déjà traitées en surface.
2.4. Dépôt Électrolytique | Technique d’Électrodéposition
La Dépôt Électrolytique, également appelée Électrodéposition est une autre technique de revêtement que vous pouvez appliquer. Avec l’aide du courant électrique, une couche protectrice est déposée sur vos pièces métalliques.
Pour que cela fonctionne, la configuration doit être composée d’un matériau conducteur plongé dans une solution saline. Votre solution doit contenir un sel du métal que vous désirez voir déposé sur la surface de votre pièce par le biais d’un courant électrique.
Après un processus de revêtement de surface réussi, vous retirez votre pièce de la solution pour un rinçage et un séchage adéquats.
3. Métaux Adaptés au Revêtement de Conversion Chimique par Film
Voici quelques-uns des métaux les plus courants sur lesquels vous pouvez appliquer avec succès un revêtement chimique par film :
3.1. Aluminium
La fabrication d’aluminium reste populaire parmi les ingénieurs et les fabricants de pièces métalliques en raison de ses propriétés favorables.
Si vous laissez la surface de votre aluminium ou de son alliage non protégée, elle s’oxydera facilement. Le chromate chimique est un processus couramment utilisé de revêtement de conversion que vous pouvez adopter pour protéger des pièces telles que des panneaux et des boîtiers contre les effets de la corrosion.
Cela prépare également vos composants pour des finitions de peinture ou de revêtement en poudre.
3.2. Cuivre
Le cuivre est un autre métal qui peut bénéficier d’un revêtement chimique par film. Étant un métal mou, il peut s’éroder rapidement si vous ne fournissez pas la protection de surface requise.
3.3. Acier Inoxydable
Votre composant en acier inoxydable peut rouiller et corroder, surtout s’il a une faible teneur en chrome.
Pour protéger sa surface de la corrosion, vous devez adopter un processus de revêtement chimique spécial appelé passivation.
Pour cela, vous devez nettoyer la surface de votre acier inoxydable avec de l’acide citrique ou nitrique.
Cela aide à éliminer le fer libre à la surface de votre composant et à permettre au chrome de réagir rapidement avec l’oxygène.
La couche formée d’oxyde de chrome qui donne à l’acier inoxydable son brillant standard assure que votre composant est efficacement protégé contre la corrosion.
3.4. Titane
Le titane, bien connu pour sa résistance supérieure, peut graduellement souffrir de corrosion, surtout lorsque votre composant est utilisé dans des environnements hostiles.
Le revêtement chimique par film est un moyen parfait de protéger vos pièces en titane de la corrosion.
3.5. Magnésium
Connu pour sa légèreté et sa solidité, le magnésium est sujet à la corrosion lorsqu’il est laissé exposé. Le revêtement chimique par film est utile pour garantir que votre aluminium est à l’abri des dégradations causées par la corrosion.
4. Types Courants de Revêtements Chimiques par Film
4.1. Revêtements de conversion au chromate
Le revêtement de conversion au chromate, également appelé revêtement Alodine, est un processus de revêtement par film chimique rentable dans lequel une solution de chromate réagit avec votre composant en métal pour former une couche protectrice à base de chrome, résistante à la corrosion.
La couche protectrice formée vous offre également une surface parfaite pour la peinture ou le revêtement en poudre.
Le revêtement de conversion au chromate est couramment utilisé sur les alliages d’aluminium, mais vous pouvez également l’appliquer pour passiver d’autres métaux.
4.2. Revêtements de conversion au phosphate
Il s’agit d’une autre catégorie de revêtement de film chimique où vous utilisez un acide phosphaté comme solution chimique de conversion.
Cela forme une couche protectrice et résistante à la corrosion d’aluminium, de phosphates de fer, de zinc ou de manganèse.
Comme la conversion au chromate, la conversion au phosphate vous fournit également une surface à haute adhérence adaptée à la peinture ou à d’autres processus de revêtement secondaire.
4.3. Revêtement d’anodisation
Le revêtement d’anodisation est un processus électrolytique de création d’une couche résistante à la corrosion sur une surface métallique.
Vous adoptez cette technique lorsque vous souhaitez améliorer la résistance à la corrosion, à l’abrasion et à l’isolation électrique ou thermique de vos composants. Plus d’informations sur l’anodisation plus tard dans cet article.
4.4. Revêtements de passivation
Le revêtement de passivation est une forme de processus de revêtement par film chimique que vous initiez après que votre composant a subi le processus de fabrication CNC ou d’autres opérations d’usinage.
Si vous travaillez sur de l’acier inoxydable, par exemple, ses surfaces sont susceptibles de contenir du fer libre qui facilite la rouille.
La passivation implique l’utilisation d’acide nitrique ou citrique pour réagir avec votre pièce usinée afin de former un oxyde résistant à la rouille. Le revêtement de passivation est donc le processus d’élimination de tels risques ou éléments de corrosion potentiels.
Selon le moment où le processus de revêtement est effectué, vous pouvez toujours vous référer en toute sécurité à certains des revêtements déjà discutés ci-dessus en tant que processus de revêtement de passivation.
5. Alodine et Anodisation – Exigences, Types, & Classes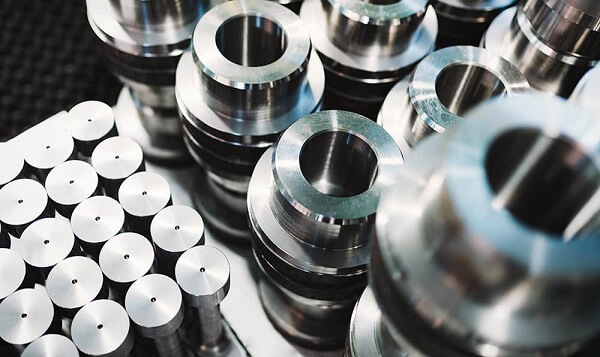
Alodine est également connu sous le nom de revêtement de conversion au chromate, iridite, chromate d’aluminium ou film chimique. Il consiste à laisser une solution de conversion chimique réagir avec votre pièce métallique pour former une fine couche d’oxyde résistante à la corrosion et à l’usure.
Les principaux ingrédients chimiques dont vous avez besoin sont le trioxyde de chrome et l’acide sulfurique.
Alodine est principalement associé au revêtement d’aluminium et est également appelé film chimique ou chromate d’aluminium.
Le film chimique peut être adopté si vous ne prévoyez pas de peindre la surface de votre composant, ou si vous devez préparer vos pièces pour la peinture ou le revêtement. Cela aide à améliorer l’adhérence pour vos besoins de revêtement secondaire.
5.1. Alodine | Revêtement de film chimique – Type 1 et Type 2
Alors qu’il existe différentes normes de revêtement de film chimique, les deux principales que vous devriez connaître sont le Type 1 et le Type 2 qui relèvent de la norme MIL-DTL-5541.
Qu’est-ce qui les différencie? Découvrons-le…
5.1.1. Film chimique – Type 1 MIL-DTL-5541
Il s’agit d’un revêtement de film chimique épais qui possède une couche de combinaison de chrome hexavalent. Il donne à votre pièce une finition de surface dorée ou brune.
Les ingrédients chimiques de votre solution Alodine sont le trioxyde de chrome et l’acide sulfurique (pour former de l’acide chromique).
Outre la résistance à la corrosion et à l’usure, vous trouverez sa finition assez attrayante.
Le principal inconvénient du revêtement de type 1 est qu’il n’est pas respectueux de l’environnement. Il produit des déchets dangereux, ce qui rend son application réglementée.
5.1.2. Revêtement de film chimique – Type 2 MIL-DTL-5541
Le Type 2 est un revêtement de film chimique mince ou revêtement de conversion au chromate qui peut contenir du chrome trivalent, du titane ou du zirconium.
Deux de ses ingrédients de revêtement chimique sont le sulfate de chrome et le chlorure de chrome.
Parce qu’il est exempt d’hexa, son adoption est populaire dans un large éventail d’industries.
La surface du revêtement de Type 2 Alodine est résistante à la corrosion et aux rayures.
Il est également esthétiquement attrayant. Il s’agit d’un processus de film chimique peu coûteux et facile à réaliser. Le revêtement forme une surface parfaite pour une finition de peinture ou de revêtement en poudre secondaire.
5.1.3. Avantages du Type 2 Alodine par rapport au Type 1
Voici quelques-uns des avantages qui font du revêtement de Type 2 Alodine bien meilleur que l’ancienne option de Type 1 :
Beaucoup plus sûr | Pas de déchets dangereux
Contrairement au Type 2 Alodine qui contient du chrome hexavalent dangereux, le revêtement de Type 2 est exempt d’hexa, respectueux de l’environnement. Cela en fait un choix parfait pour les fabricants d’aluminium modernes.
Fonctionne à température ambiante
Vous pouvez entreprendre le processus de revêtement de film chimique de Type 2 à température ambiante sans avoir besoin de cuves de chaleur énergivores. Cela vous permet d’économiser considérablement sur vos factures d’électricité.
Application plus rapide et plus facile
Comparé au revêtement de Type 1, le revêtement de Type 2 Alodine est beaucoup plus rapide car il nécessite moins d’étapes de traitement.
5.2. Revêtement Alodine – Classe 1A & Classe 3
Rappelez-vous que lorsqu’il s’agit de classes de revêtement Alodine ou de film chimique, votre attention doit être portée sur les domaines d’application des revêtements de type 1 et de type 2.
Il s’agit d’une classification de leurs domaines d’exigence. Maintenant, avec cette clarification, découvrons ce que chaque classe apporte à votre table d’application !
5.2.1. Revêtement de film chimique – Classe 1A | Normes Alodine 1200
Les revêtements de film chimique avec une couche protectrice de type 1 Alodine relèvent des normes de spécification de Classe A ou sont généralement appelés Alodine 1200.
Il vous offrira une protection de surface supérieure contre la corrosion, que vos composants aient ou non des revêtements secondaires.
5.2.2. Film chimique Alodine Classe 3 | Spécifications Alodine 1500
En termes de normes, les revêtements de type 2 relèvent de la Classe 3 et vous pouvez également les appeler Alodine 1500.
Alodine de Classe 3 est un choix de revêtement de film chimique parfait si vous recherchez une surface résistante à la corrosion mais avec une faible résistance thermique ou électrique.
5.2.3. Tableau récapitulatif de la norme MIL-DTL-5541 montrant les types et classes d’Alodine
Norme MIL-DTL-5541 | Type 1 – Alodine | Type 2 – Alodine |
Type de revêtement de film de chromate | Chromate hexavalent | Finition au chromate tétravalent (sans hexa) |
Classe 1A (Alodine 1200) | Offre une résistance supérieure à la corrosion. Peut être utilisé avec ou sans un revêtement secondaire | Offre une résistance supérieure à la corrosion. Peut être utilisé avec ou sans un revêtement secondaire |
Classe 3 (Alodine 1500) | Résistant à la corrosion avec une conductivité thermique/électrique améliorée | Résistant à la corrosion avec une conductivité thermique/électrique améliorée |
6. Alodine vs. Revêtements d’anodisation – Comparaisons
La principale différence entre les deux revêtements de conversion est qu’avec l’anodisation, vous devez faire passer de l’électricité à travers un électrolyte (processus électrolytique), ce qui n’est pas le cas pour le revêtement Alodine/film chimique.
Maintenant, afin que vous ne confondiez pas le processus de revêtement de film chimique à l’aluminium Alodine avec l’aluminium anodisé (processus électrochimique), comparons les similitudes et les différences que ces deux processus uniques ont.
6.1. Similitudes
Les couches protectrices résistantes à la corrosion : Tant l’alodine que l’anodisation de l’aluminium ont des couches de surface protectrices résistantes à la corrosion.
Fonctionne sur l’aluminium et d’autres métaux : Les revêtements d’alodine et anodisés sont principalement utilisés sur l’aluminium mais peuvent fonctionner sur d’autres métaux non ferreux.
Manipulation sûre des produits chimiques : Les deux processus impliquent l’utilisation de solutions chimiques. Par conséquent, les deux nécessitent que vous preniez les précautions de sécurité nécessaires.
Exigences en matière de compétences et d’équipement : Les deux processus nécessitent que vous ayez les compétences et l’équipement nécessaires pour des résultats parfaits.
6.2. Différences :
Processus de revêtement : Contrairement au revêtement d’alodine, l’anodisation est un processus de revêtement métallique électrolytique.
Coût et exigences en matière de compétences : Le revêtement d’alodine est un processus plus rentable avec moins d’exigences en équipement ou en main-d’œuvre. Avec le processus d’anodisation, vous devez creuser plus profondément dans vos poches pour obtenir le bon équipement et le personnel qualifié.
Propriétés thermiques et électriques : Le revêtement d’alodine offre moins de résistance à l’électricité que les surfaces anodisées.
Options de teinture | Esthétique : Avec l’alodine, vos choix de couleur sont limités au marron ou transparent. L’anodisation vous offre une option pour plus de couleurs pour une esthétique améliorée.
Épaisseur des couches de surface : Avec le processus d’alodine, vous obtenez une couche résistante à la corrosion plus mince mais avec une grande tolérance, tandis que l’anodisation vous donne une couche plus épaisse qui est un revêtement plus résistant à la corrosion.
7. Processus de revêtement chimique en film
Alors que les processus de revêtement chimique en film varient en fonction de leurs différents types de conversion, voici les trois principales étapes impliquées :
7.0.1. Étape de préparation
Avant de commencer tout processus de revêtement chimique en film, vous devez vous assurer de nettoyer votre matériau avec le détergent le plus approprié.
Pour vos pièces usinées, vous pouvez opter pour un détergent acide ou alcalin approprié pour les revêtements d’alodine de type 1 et de type 2 respectivement.
Votre connaissance de la méthode la plus appropriée pour nettoyer les pièces usinées en CNC est cruciale. Cela est dû au fait que les pièces usinées ont toujours beaucoup de contaminants nuisibles qui doivent être éliminés efficacement.
Après le processus de nettoyage, votre pièce doit être séchée. Vous devez vérifier minutieusement le composant pour vous assurer qu’il est exempt de défauts.
Si des défauts sont détectés, vous devez entreprendre les réparations nécessaires avant de continuer avec votre processus de revêtement de conversion.
7.0.2. Étape d’application du film chimique
Lorsque votre matériau est propre, sec et en parfait état, vous pouvez alors commencer votre processus de revêtement chimique en film.
Vous pouvez également plonger votre pièce fabriquée dans une solution d’alodine de type 1 ou de type 2, ou adopter un processus électrolytique ou d’anodisation jusqu’à ce que l’épaisseur de couche désirée soit formée. Ce processus peut prendre entre 1 et 3 minutes.
7.0.3. Étape de durcissement du film chimique
Une fois que l’épaisseur désirée de votre couche de film chimique est formée, vous devez rincer le matériau. Si votre revêtement est à base de chromate, laissez-le reposer jusqu’à 24 heures pour que le revêtement durcisse complètement.
Vous pouvez accélérer le processus en chauffant le matériau, mais assurez-vous que la température de chauffage ne dépasse pas 70 degrés Celsius (158 degrés Fahrenheit). Un durcissement à des températures plus élevées a l’effet inverse de dégrader votre couche protectrice.
7.1. Processus de revêtement chimique en film Alodine de type 1 et de type 2
7.1.1. Processus de conversion au chromate de type 1
Pour une finition au chromate de type 1 ou hexavalent, les principales étapes du processus sont les suivantes.
Étape 1 : Nettoyage des composants
Nettoyer votre composant avec de l’eau propre et un détergent doux approprié est une étape de préparation importante. Elle vise à s’assurer que votre pièce métallique est exempte de contaminants tels que la poussière, la saleté, l’huile et toute autre particule résultant du processus d’usinage.
Étape 2 : Rinçage et séchage
Après le nettoyage, rincez votre pièce métallique à l’eau propre et laissez-la sécher. Vous pouvez utiliser diverses approches de séchage, comme le séchage à l’air ou à l’aide d’un souffleur d’air.
Étape 3. Attaque alcaline
Utilisez de l’hydroxyde de sodium pour attaquer votre pièce en aluminium ou en métal afin de la préparer au revêtement de film chimique.
Étape 4. Rinçage
Rincez les composants à l’eau propre
Étape 5: Désoxydation et dégraissage
Utilisez un désoxydant approprié, tel que de l’acide nitrique doux ou toute autre combinaison adaptée, pour éliminer la couche d’oxydation et laisser votre pièce métallique fraîche et brillante.
Étape 6. Rinçage
Rincez votre pièce métallique désormais prête
Étape 7. Revêtement de film chimique
Maintenant, plongez la pièce dans votre solution de revêtement chromaté qui est de l’acide chromique pendant 5 minutes
Vous pouvez également brosser votre pièce ou la vaporiser avec la solution de revêtement de film chimique.
Étape 8. Rinçage
Retirez et rincez votre pièce métallique fraîchement revêtue pour arrêter tout processus d’attaque supplémentaire
Étape 9. Rinçage à l’eau chaude
Pour un nettoyage renforcé et une finition de qualité sur votre composant.
Remarque : Assurez-vous toujours de faire un test de rupture d’eau pour vous assurer que votre pièce est exempte de contaminants.
7.1.2. Processus de revêtement de film chimique de conversion au chromate de type 1 | Alodine
Pour la finition Alodine de type 2, les deux processus sont la méthode de nettoyage acide et la méthode de nettoyage alcalin
Processus de nettoyage acide
Le processus de nettoyage acide se compose des étapes suivantes :
- Nettoyez votre pièce métallique avec un acide doux
- Rincez et utilisez de l’eau propre pour rincer la pièce pour vous assurer qu’elle est exempte de tout acide
- Appliquez des produits chimiques de revêtement tels que du chrome tétravalent, du titane ou du zirconium par immersion, brossage ou pulvérisation selon le cas
- Rincez à l’eau propre pour éliminer l’excès de produit chimique de revêtement
- Deuxième rinçage pour un nettoyage renforcé
- Laissez sécher et durcir pendant au moins 24 heures.
Processus de nettoyage alcalin
- Nettoyez avec une solution alcaline – Hydroxyde de sodium
- Rincez à l’eau propre
- Désoxydez avec un acide doux pour attaquer la surface métallique
- Rincez à l’eau claire
- Appliquez une solution de revêtement chimique sans hexavalent
- Rincez pour enlever les excès de produits chimiques
- Deuxième rinçage
- Laissez sécher et durcir pendant au moins 24 heures
Remarque :Après avoir rinçé vos pièces, vous devriez faire un test de l’eau pour vous assurer que votre pièce est exempte de contaminants avant de passer à l’étape suivante. Plus de détails sur le processus sont couverts dans la réparation et la maintenance
8. Revêtement chimique – Avantages, avantages et inconvénients.
8.1 Avantages et avantages
Voici certains des principaux avantages que vous obtiendrez en adoptant le revêtement chimique, en particulier sur vos pièces en aluminium :
Coût-efficace et Application facile/rapide.
Les méthodes d’application du revêtement chimique par immersion, pulvérisation ou brossage sont faciles et rentables. Vous n’avez pas besoin de dépenser pour des équipements coûteux. Son application est également beaucoup plus rapide que d’autres processus tels que la peinture ou les options d’anodisation.
h4>Résistance accrue à la corrosion et à l’usure | Améliore la durabilité
Le revêtement chimique durcit les surfaces de vos composants et les rend ainsi résistants à la corrosion et à l’usure. Cela améliore leurs performances dans des conditions environnementales difficiles.
Avec la couche de protection de vos pièces, leur durabilité sera considérablement améliorée.
h4>Amélioration de la lubrification de surface | Porteur de lubrification
Le revêtement chimique améliore la lubrification de surface de vos composants. Cela aide à réduire les frottements et l’usure, améliore les performances et réduit vos coûts de maintenance.
h4>Réduction de la porosité de la surface métallique
Les métaux techniques tels que l’aluminium, le cuivre et le magnésium, entre autres, sont connus pour être poreux. Le revêtement chimique aide à sceller leurs surfaces contre les éléments environnementaux agressifs. Cela rend également les surfaces de vos pièces plus lisses et attrayantes.
h4>Apprêt pour la peinture organique ou la poudre de revêtement | Améliore l’adhérence
Si vous envisagez de donner à votre composant usiné une peinture parfaite ou un revêtement en poudre, alors le revêtement chimique est un apprêt efficace ou une sous-couche pour votre travail de peinture final.
Le revêtement améliore l’adhérence pour garantir que vos peintures ou revêtements en poudre adhèrent solidement à votre pièce métallique et durent plus longtemps !
h4>Couche mince pour des tolérances strictes
Si votre pièce finale a une forme complexe et est destinée à être utilisée dans des zones où très peu de tolérance est souhaitée, ne vous inquiétez pas.
Les revêtements chimiques sont minces et n’affecteront donc pas négativement l’application de votre composant.
h4>Capacité de travailler sur de grands composants
La simplicité de la technique de revêtement chimique vous permet de travailler facilement et à moindre coût sur des composants pouvant mesurer jusqu’à 144 pouces (12 pieds).
Étant donné que l’immersion peut être difficile pour les pièces de grandes tailles, il vous suffit de pulvériser ou de brosser vos pièces avec une solution de conversion chimique appropriée.
h4>Conductivité thermique et électrique améliorée
Les revêtements chimiques laissent une fine couche de surface avec des niveaux améliorés de conductivité thermique et électrique. Cela rend le processus idéal pour une utilisation dans des produits tels que les dissipateurs de chaleur.
h4>Capacité de traiter de grands volumes
Étant donné que le processus de revêtement chimique est facile et rapide, vous pouvez travailler sur plusieurs pièces en très peu de temps. Par conséquent, traiter des pièces en grands volumes pour répondre aux exigences des commandes ne sera pas votre principale préoccupation.
8.2 Inconvénients du revêtement chimique
Voici quelques inconvénients que vous êtes susceptible de rencontrer lors de l’utilisation des techniques de revêtement chimique :
h4>La phase de préparation peut être coûteuse
Une préparation adéquate est requise avant d’entreprendre le processus de revêtement chimique, ce qui peut être coûteux en termes de matériaux et d’équipements nécessaires.
N’oubliez pas que la phase de préparation comprend également le processus de nettoyage initial.
h4>Vulnérable aux rayures
Parce que le revêtement de conversion au chromate est une fine couche de protection par rapport aux surfaces anodisées, les surfaces de vos composants seront vulnérables aux rayures ou aux forces d’abrasion.
Cela dégrade progressivement leur résistance à la corrosion tout en leur faisant perdre leur attrait esthétique beaucoup plus rapidement.
h4>Les produits chimiques utilisés sont toxiques | Risques dangereux
Les solutions chimiques utilisées dans le revêtement chimique peuvent être dangereuses pour votre peau et vos yeux et nécessitent des mesures de sécurité lors de la manipulation. Le revêtement de chrome hexavalent est réglementé car il est dangereux.
h4>Choix limité de couleurs souhaitées
Alors qu’avec un processus d’anodisation, vous pouvez obtenir une large gamme de couleurs de surface, le processus de revêtement chimique ne vous offre pas un tel luxe.
Les couleurs possibles sont limitées au brun ou à l’or pour la couche de chrome hexavalent et une finition transparente pour la finition de chrome trivalent.
h4>Retrait de la couche difficile lors de l’entretien
Parfois, vos tâches de maintenance ou de réparation peuvent nécessiter que vous enleviez les revêtements chimiques de vos composants. Vous trouverez cela exigeant et chronophage.
h4>Augmente l’isolation thermique
Dans certaines zones, le maintien de la température est critique. Si vos composants doivent être utilisés ou installés dans de telles zones, leur revêtement chimique, en particulier de Type 2, peut créer une couche d’isolation thermique indésirable.
h4>Surface sujette aux dommages mécaniques
Si vos pièces doivent être exposées à des forces mécaniques, leurs revêtements chimiques seront facilement endommagés par des forces abrasives.
Dans de telles situations, vous devez envisager d’autres options de revêtement secondaire pour gérer efficacement les risques potentiels et garantir la durabilité souhaitée.
9. Normes et spécifications – Revêtements chimiques d’alliage d’aluminium
Les normes de revêtement chimique font référence à des catégories de revêtements de conversion dont les spécifications conviennent à des applications industrielles particulières.
Le tableau ci-dessous montre certaines des normes de revêtement de conversion les plus couramment utilisées que vous, en tant que fabricant, devez connaître.
Norme | Description de la spécification |
MIL-DTL-5541 | Une spécification militaire couramment utilisée pour le revêtement chimique sur l’aluminium et ses alliages. De différents types et classes. la norme utilisée par ceux qui entreprennent des processus de conversion chimique tels que les fabricants de métaux |
MIL-DTL-81706 | Couramment utilisé sur l’aluminium et ses alliages. Utilisé pour la fabrication de produits chimiques de revêtement de conversion. |
AMS 2474 | Spécification aérospatiale pour les traitements des alliages d’aluminium où une faible résistance thermique ou électrique est souhaitée |
ASTM B449 | Norme pour les chromates d’aluminium utilisés comme apprêt ou base pour les revêtements organiques secondaires |
ASTM B921 | La spécification standard s’applique à la finition sans hexavalent Alodine (sur de l’aluminium ou des alliages d’aluminium). Les spécifications partagent certaines similitudes avec le Type2 -MIL-DTL-5541 |
ISO 8081 | Norme de spécification aérospatiale pour le revêtement chimique de conversion polyvalent pour l’aluminium et ses alliages d’aluminium. Met l’accent sur les exigences standard pour la production et les tests de revêtements de conversion chimique. |
AMS-2473 | Norme de spécification aérospatiale pour le revêtement polyvalent des alliages de base en aluminium, similaire à la Classe 1A MIL-DTL-5541 |
BAC 571 | Spécification Boeing sur les processus de revêtement chimique impliquant de l’aluminium et des alliages d’aluminium. La norme présente certaines similitudes avec la norme MIL-DTL-5541. |
10. Applications de l’industrie des revêtements chimiques
10.1. Industrie Aérospatiale
Les parties externes des avions sont exposées à une large gamme de conditions météorologiques extrêmes tant au sol que dans les airs.
Ainsi, le revêtement chimique est utilisé pour leur offrir une protection efficace contre la corrosion et l’abrasion. Cela limite l’usure et améliore la durabilité.
10.2. Industrie Maritime
Vous trouverez que le revêtement chimique est important pour protéger l’aluminium, l’acier inoxydable et d’autres pièces métalliques utilisées dans l’industrie maritime.
Des pièces telles que la coque et les hélices, entre autres, nécessitent des revêtements chimiques pour résister à la corrosion de surface, exposées à des environnements marins agressifs.
10.3. Application dans l’industrie électrique
Si vos pièces électriques telles que les fils ou les connecteurs ne possèdent pas de couches protectrices sur leurs surfaces, elles seront sujettes à la corrosion et à l’usure.
Grâce aux revêtements chimiques, vous les protégez contre divers dangers environnementaux tels que l’eau et l’humidité.
10.4. Applications Militaires et de Défense
Les armes et équipements militaires métalliques sont conçus pour être utilisés dans différentes conditions météorologiques. Grâce aux revêtements chimiques, ils sont protégés contre les conditions météorologiques extrêmes qui les exposeraient à la corrosion et à l’usure.
10.5. Parties de l’Industrie Architecturale
Vos composants architecturaux ou matériels métalliques sont exposés à la corrosion s’ils sont exposés aux éléments externes.
Le processus de revêtement chimique garantit qu’ils sont adéquatement protégés pour la durabilité et l’esthétique désirées.
10.6. Industrie Automobile
Dans l’industrie automobile, des processus de revêtement chimique tels que les revêtements de conversion au zirconium et au titane ont gagné en popularité pour leur résistance à la corrosion et leur adhérence améliorée à la peinture.
11. Réparation et Maintenance – Finitions Alodine et Anodisées
11.1. Maintenance Générale des Revêtements Chimiques
Les revêtements chimiques tels que Alodine ou les surfaces anodisées nécessitent un entretien à la fois lors de leur installation et périodiquement par la suite.
Lorsque vos pièces telles que l’aluminium architectural ou d’autres composants de construction anodisés sont négligés sans un entretien approprié, leurs couches protectrices peuvent être compromises progressivement.
Pour garantir leur durabilité, un nettoyage périodique pour éliminer la saleté et la poussière accumulées est important. Sinon, ils facilitent l’altération des surfaces de vos composants.
Pour les structures externes telles que l’aluminium architectural, un nettoyage tous les 12 mois est recommandé.
Cependant, si vos structures ou pièces sont exposées à des conditions météorologiques extrêmes, envisagez de les nettoyer plus fréquemment à l’aide d’un savon doux pour maintenir leur état.
Assurez-vous que votre méthode de nettoyage est adaptée à votre type de finition.
Pour plus de ressources sur la meilleure manière de nettoyer vos finitions anodisées, consultez ici.
11.2. Réparation de Votre Revêtement Chimique
En tant que fabricant de métaux, vos clients peuvent demander des réparations sur les revêtements chimiques sur un large éventail de pièces. Vous pouvez également effectuer une réparation pour corriger les défauts sur vos pièces nouvellement revêtues.
Le niveau d’entretien ou de réparation requis pour vos pièces est déterminé par la conception de la pièce, le type de revêtement qu’elle possède (Alodine ou anodisé), l’âge du revêtement et le niveau de défauts de surface.
Vous devez respecter toutes les précautions de sécurité nécessaires lors de votre processus de réparation ou d’entretien.
Étant donné que vous manipulerez des produits chimiques acides, vous devez porter les équipements de sécurité appropriés tels que des gants résistants aux produits chimiques, des lunettes de protection et un manteau long.
Alors, comment évaluez-vous si votre pièce nécessite un entretien ou une réparation ?
Si votre réponse est oui aux questions suivantes, alors la surface métallique est défectueuse et nécessite un entretien ou une réparation :
- La surface semble-t-elle lâche et poudreuse ?
- La couche de revêtement de la surface semble-t-elle irrégulière ?
- Votre surface métallique paraît-elle terne en couleur ?
- La pièce a-t-elle échoué au test de brouillard salin ?
Note: Si votre pièce métallique est peinte, utilisez le produit chimique recommandé pour enlever la couche de peinture. Pour une surface laquée, envisagez la méthode la plus appropriée pour enlever la couche de poudre avant de procéder.méthode pour enlever la couche de poudre avant de continuer.
11.2.1. Réparation des égratignures fines et mineures
Il arrive parfois que votre revêtement de film chimique présente des égratignures fines qui lui donnent un aspect moins esthétique.
Vous pouvez les réparer en nettoyant la surface, en la laissant sécher, puis en appliquant un produit de polissage fin ou un composé de lustrage adapté.
Veillez à ne pas utiliser de nettoyants abrasifs car ils peuvent facilement endommager la fine couche protectrice de votre composant.
11.2.2. Réparation du revêtement de film chimique endommagé/Alodine
Avant de procéder à toute réparation sur un revêtement de film chimique endommagé, identifiez si la finition est une finition alodine ou anodisée.
Si les dommages sur la surface affectent également le métal, concentrez-vous sur l’élimination de l’ensemble de la couche de revêtement pour vous permettre de réparer la surface métallique avant de la préparer pour un nouveau processus de conversion chimique.
Les étapes de réparation sont les suivantes :
1. Nettoyage de la surface
Nettoyez soigneusement votre composant avec une méthode de nettoyage appropriée telle qu’un nettoyant solvant ou un nettoyant abrasif.
Cela est nécessaire pour garantir que la surface du composant est exempte de saleté ou de contaminants.
2. Préparation de la surface – Attaque acide | Retrait de la couche Alodine
Retrait du revêtement Alodine frais
Cela implique de retirer la couche défectueuse de finition Alodine sur vos pièces. Si vous réparez une nouvelle finition Alodine 1200 ou la nouvelle Alodine 1500 améliorée, il vous suffit d’immerger la pièce dans de l’acide nitrique 1: 1.
Attendez environ 5 minutes puis retirez, rincez et séchez la pièce.
Retrait de la finition Alodine ancienne
La finition Alodine ancienne est difficile à enlever. Pour y parvenir avec succès, votre pièce a besoin d’une attaque alcaline suivie d’un bain acide
Traitement alcalin: Vous plongez votre pièce dans de l’hydroxyde de sodium (soude caustique) avec une concentration de 100 à 150 g/l.
Pour faciliter le processus de décapage, une température comprise entre 104°F et 140°F est recommandée.
Traitement acide: Après le décapage, plongez-la dans une solution d’acide nitrique de 30% à 50% pour le dégraissage et éliminer les impuretés.
Note : L’utilisation excessive de l’acide de décapage peut endommager votre surface métallique. Les déchets des revêtements hexavalents sont dangereux et doivent être manipulés et éliminés avec soin.
3. Solution Alodine – Traitement du revêtement de film chimique
Plongez la pièce à réparer dans une solution Alodine adaptée. Vous pouvez également appliquer la solution à l’aide d’un pinceau ou par pulvérisation. Attendez quelques minutes que le revêtement sèche.
Note : La solution de revêtement de conversion chimique à utiliser pour votre réparation dépend du type de revêtement de film chimique que vous souhaitez appliquer.
4. Nettoyez/Rincez la surface
Nettoyez et rincez votre pièce et laissez-la sécher.
5. Durcissement
Attendez jusqu’à 24 heures que la pièce durcisse complètement et soit prête à être utilisée. Vous pouvez également raccourcir la période de durcissement en exposant la pièce à la plage de température spécifiée pour votre revêtement.
Les températures de durcissement que vous définissez doivent correspondre aux spécifications du revêtement de film chimique que vous appliquez.
Par exemple, si votre finition de film chimique est Alodine 1200, réglez la température de durcissement entre 40 et 70 degrés Fahrenheit. Pour Alodine 1500, réglez les températures entre 70 et 160 degrés Fahrenheit.
Note : Le réglage de températures plus élevées que les niveaux recommandés impactera négativement votre revêtement réparé.
Après le durcissement, votre composant est prêt pour d’autres revêtements secondaires si nécessaire, ou prêt pour une application telle quelle.
11.3. Réparation d’un métal anodisé endommagé
Pour les travaux de réparation sur des composants en aluminium anodisé, vous devez être conscient des différents types de processus d’anodisation de l’aluminium.
Votre connaissance vous guidera pour identifier l’approche la plus appropriée pour réparer toute finition anodisée endommagée.
Ainsi, bien que les directives de réparation que nous détaillons ici soient générales et plus axées sur les alliages d’aluminium, il est important que votre processus de réparation soit basé sur une finition anodisée particulière et souhaitée.
Obtenir les bonnes directives de réparation et de maintenance auprès du fournisseur de la pièce ou des détails de spécification vous guidera sur la meilleure façon de réaliser la réparation.
Généralement, réparer une pièce anodisée endommagée n’est pas aussi simple que celle d’une finition Alodine. Le revêtement est extrêmement difficile à enlever.
Donc, si seule une section est endommagée, vous pouvez masquer la partie non affectée et ensuite réparer la partie endommagée.
11.3.1. Réparation du revêtement de film chimique – Égratignures mineures sur la surface anodisée.
- Masquez la partie de votre pièce anodisée qui n’est pas affectée par les égratignures de surface.
- Appliquez de l’hydroxyde de sodium sur la partie affectée pour enlever le revêtement d’oxyde métallique
- Rincez votre pièce à l’eau désionisée pour éliminer l’hydroxyde de sodium
- Démarrez un nouveau processus d’anodisation en utilisant de l’acide sulfurique ou de l’acide chromique
- Appliquez la tige de cathode sur la surface métallique à anodiser
- Attendez que l’épaisseur de l’oxyde métallique formé corresponde à celle de la surface non affectée.
- Retirez et rincez la pièce.
11.3.2. Réparation du revêtement de film chimique – Endommagé à la fois le métal et la couche anodisée
Pour des dommages importants à la fois sur la finition anodisée et le substrat métallique, vous devez enlever l’ensemble de la couche anodisée, réparer la surface métallique et la re-anodiser à neuf.
Le premier processus après avoir nettoyé et séché votre pièce endommagée en surface consiste à retirer la couche anodisée, ou à enlever son revêtement d’oxyde métallique. Cela est suivi d’un processus de re-anodisation.
Voici les étapes générales du processus de réparation du métal et de la finition anodisée :
- Nettoyez le composant sur lequel vous devez travailler et laissez-le sécher
- Versez de l’eau désionisée dans un récipient en acier inoxydable adapté
- Chauffez le liquide au gaz à une température comprise entre 140 et 160 degrés Celsius
- Ajoutez de l’acide nitrique et oxalique à l’eau “ID” déjà chauffée
- Immergez votre pièce endommagée dans le mélange acide
- Laissez les pièces pendant environ 15 minutes. La couche d’oxyde métallique sera enlevée
- Retirez les pièces et rincez-les à l’eau désionisée fraîche
- Réparez la surface métallique endommagée en utilisant des méthodes appropriées pour garantir qu’elle est sans rayures
- Initiez un nouveau processus d’anodisation en appliquant la tige de la cathode à toute la pièce métallique
- Attendez que l’épaisseur d’oxyde métallique désirée soit atteinte
- Retirez et rincez vos pièces métalliques entièrement réparées et anodisées.
Note : Différents types de finitions anodisées peuvent nécessiter différentes approches de réparation. Assurez-vous que la méthode que vous adoptez est adaptée et recommandée pour votre alliage métallique spécifique ou votre type de surface anodisée.
12. Conclusion
Le revêtement de film chimique ou le revêtement de conversion est un processus de fabrication essentiel qui garantit la protection efficace de vos pièces pour leur performance efficace et à long terme.
Les deux principaux processus de revêtement de conversion sont le processus de conversion de chromate et l’anodisation. Ainsi, votre sélection du bon processus de revêtement de film chimique ou de réparation doit être basée sur le type de composant métallique sur lequel vous travaillez, son application et le revêtement protecteur souhaité.
Le revêtement de chromate de type 1 est un processus simple si votre pièce nécessite une couche anticorrosion mince et moins résistante à l’électricité.
Cependant, en raison de ses restrictions sur l’utilisation du chrome hexavalent dangereux, son utilisation a continué de décliner en raison des restrictions imposées à son utilisation.
Cependant, la finition Alodine de type 2 est exempte d’hexavalent et respectueuse de l’environnement. Par conséquent, elle continue d’être populaire et est le choix idéal pour vos projets de fabrication d’aluminium architecturaux.
L’anodisation, qui est un processus électrolytique, est une autre forme de revêtement de conversion pour des couches protectrices plus épaisses, résistantes à la corrosion, résistantes à l’usure et avec une isolation thermique renforcée.
L’entretien périodique de toutes vos structures avec un revêtement de film chimique est crucial pour garantir qu’elles fonctionnent mieux et plus longtemps.
En tant que fabricant, vous devez également vous concentrer sur une connaissance approfondie de la meilleure façon de réparer les différents types de métaux anodisés, en particulier les alliages d’aluminium.
Votre connaissance complète du métal sur lequel vous travaillez, du type de revêtement de film chimique requis et des processus impliqués est critique.
Faire appel à un fabricant de métal fiable avec une connaissance et une expérience adéquates en technologie de revêtements de film chimique est la meilleure approche pour garantir que rien ne tourne mal.