Dans ce guide, nous allons comparer le processus de moulage par injection de métal par rapport au processus de moulage sous pression.
En conséquence, vous saurez quand choisir le meilleur processus pour le processus de fabrication de pièces métalliques.
Jetez un œil:
Définition : Moulage par Injection de Métal vs Moulage Sous Pression
Le moulage par injection de métal (MIM) transforme le métal sous forme de poudre en un mélange homogène.
Ce mélange de matériau fait référence à la matière première, puis il est soumis à un moulage par injection pour obtenir la forme désirée et la solidification.
Le moulage sous pression utilise du métal en fusion. Vous transformerez le métal en fusion en produit utile en utilisant un moule spécial sous haute pression. Cela vous aidera à créer les produits désirés.
Processus de Fabrication MIM Vs Processus de Moulage Sous Pression
Il y a une variation significative entre les processus de MIM et de moulage sous pression comme vous le verrez bientôt.
Processus de Moulage par Injection de Métal (MIM)
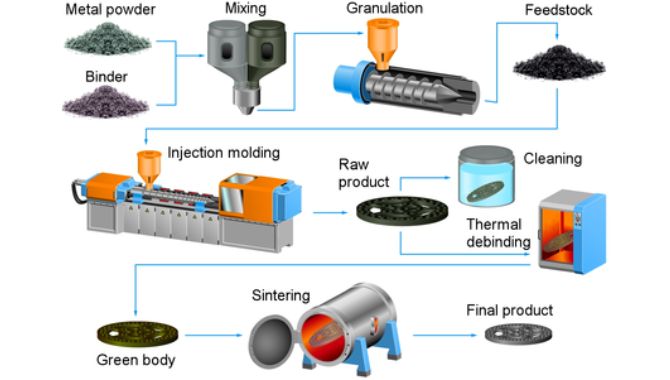
1. Préparation de la Matière Première
La préparation de la matière première est la première étape du MIM. À cette étape, la poudre métallique est mélangée avec le liant. Il est important de maintenir le ratio de poudre métallique et de liant à un ratio de 60:40.
Ensuite, il est nécessaire de mettre le mélange dans un équipement de granulation, qui chauffe d’abord le matériau pour faire fondre le liant.
Ensuite, un mélange uniforme conduit à un revêtement uniforme du liant sur le métal en poudre. Après cela, le refroidissement conduit à la formation de granules ou de pellets. Ces pellets sont ensuite utilisés dans l’étape de moulage par injection.
2. Moulage par Injection
Après la préparation de l’équipement de moulage, vous ajouterez du métal en poudre avec la solution de liant. Ensuite, chauffez les granules à haute température et injectez-les dans la cavité du moule. Le matériau y reste pendant un certain temps pour se solidifier par refroidissement successif.
3. Déliantage
Lorsque le moulage par injection se termine, vous obtiendrez le composant final. Vous devez maintenant soumettre ce composant au déliantage. Le matériau de liaison que vous avez utilisé précédemment est retiré à cette étape. La méthode d’extraction par solvant élimine le liant. La structure microscopique semi-poreuse permet au liant de s’échapper.
4. Frittage
Après le déliantage, vous devez placer le composant dans le four de frittage. Ici, le composant est soumis à beaucoup de chaleur et de retrait. Ce processus élimine tout matériau de liaison restant. Après avoir terminé cette étape, vous obtiendrez le composant avec des tolérances/dimensions précises selon les besoins.
5. Finition
La finition, en réalité, n’est pas une étape du Moulage par Injection de Métal. Mais si nécessaire, vous pouvez soumettre le composant fritté à une usinage supplémentaire. Cela peut inclure un chauffage pour obtenir les propriétés physiques désirées. Ou taillage, polissage, meulage, sérigraphie, etc., pour obtenir les tolérances ou dimensions souhaitées.
Processus de Moulage Sous Pression
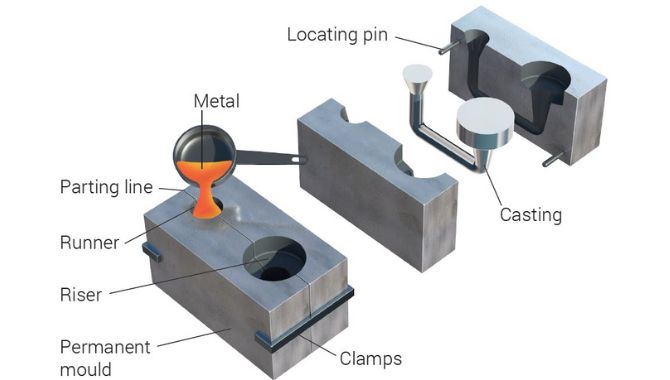
1. Préparation du Moule
La première étape implique la préparation du moule. À cette étape, vous pulvérisez un lubrifiant à l’intérieur du moule et le chauffez à une température appropriée. Ensuite, vous serrez et refermez fermement les moitiés du moule pour la suite du processus.
2. Injection
À cette étape, vous devez forcer le métal en fusion provenant du four. Vous le faites sous haute pression et température à l’intérieur du moule. De cette manière, le matériau en fusion est réparti uniformément dans tout le moule.
3. Refroidissement
Après avoir placé le métal en fusion dans le moule, vous devez le laisser un certain temps pour le processus de refroidissement et de solidification.
4. Éjection
Après la solidification, ouvrez les moitiés du moule et retirez le composant moulé. Vous pouvez utiliser vos mains ou même des broches d’éjection pour le faire.
5. Taillage
Dans la dernière étape, vous effectuez le taillage. Pendant la solidification, il y a des chances que certains matériaux se solidifient au niveau des canaux d’alimentation, des carottes, des coureurs et des éclats. Vous pouvez utiliser plusieurs outils pour éliminer toutes les particules non désirées.
Matériaux de Fabrication : Moulage par Injection de Métal vs Moulage Sous Pression
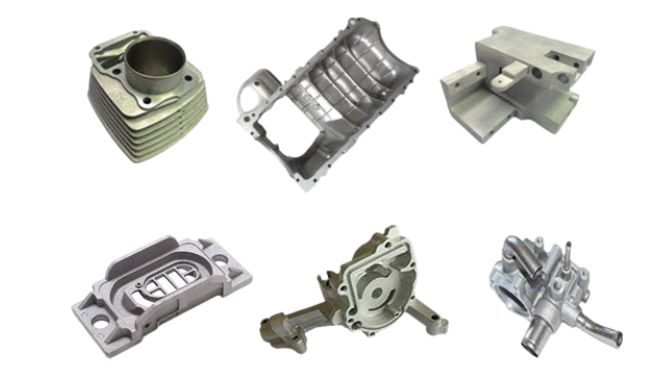
Meilleur Matériau pour le Moulage par Injection de Métal
Veuillez noter que le matériau de fabrication décide des propriétés finales du composant. Pour les processus, vous pouvez considérer ces matériaux:
Matériaux de MIM:
Nº | Matériaux | |||
Alliages ferreux | Alliages de tungstène | Matériaux durs | Matériaux spéciaux | |
1 | Acier | Alliage lourd de tungstène | Cermets | Alliage de titane |
2 | Acier inoxydable | Cuivre-tungstène | Carbures cémentés | Cobalt chrome |
3 | Alliage magnétique en fer-nickel | Molybdène | ||
4 | Invar | Cuivre-molybdène | ||
5 | Kovar | Nickel | ||
6 | Superalliage à base de nickel |
Moulage des matériaux
Le moulage utilise principalement des alliages non ferreux pour fabriquer des composants de moulage. Les matériaux courants comprennent:
Nº | Matériaux |
Alliages non ferreux | |
1 | Plomb |
2 | Étain allié |
3 | Alliage à base d’étain |
4 | Magnésium |
5 | Cuivre |
6 | Aluminium |
7 | Zinc |
Injection de métal vs moulage sous pression – Applications clés
Pièces MIM[/caption>
Exemples de pièces MIM
Nº | Applications | ||||
Armes à feu | Domaine médical | Industrie automobile | Électronique | Industrie aérospatiale | |
1 | Gréeurs | Remplacement de joint | Turbocompresseur | Radiateurs | Vis à volet |
2 | Détenteur de magasin | Engrenages | Bras de rocker | Plaques froides | Porte-valves |
3 | Extinction d’incendie | Dispositifs pour médicaments | Leviers de changement | Composants de téléphone | Composants du moteur |
4 | Sûreté | Connecteurs d’éclairage | Brûleurs de fusée | ||
5 | Composants de fibre optique |
Exemples de pièces de moulage sous pression
Nº | Applications | ||
Industrie de la pelouse / du jardin / des loisirs | Industrie médicale | Industrie automobile | |
1 | Châssis de RV | Couvercle d’ordinateur | Boîtier d’engrenage |
2 | Inserts de doublure en acier | Commandes d’équipement hospitalier | Boîtier de transmission |
3 | Contre-dépouilles marines | Dispositifs chirurgicaux | Retenues |
4 | Boîtiers d’engrenages | Pompes péristaltiques | Boîtiers de système de GPS et de divertissement |
5 | Essieux hydrostatiques | Analyseurs sanguins | Composants du moteur |
Systèmes de transmission de puissance |
Coûts d’exploitation pour l’injection de métal vs le moulage sous pression
Lors de la comparaison des coûts d’exploitation, le moulage sous pression l’emporte clairement par rapport à l’injection de métal. Pour les dépenses opérationnelles, le moulage sous pression est un processus économique.
Pour le moulage sous pression, le coût se situe dans les milliers de dollars ; pour l’injection de métal, le coût se situe dans les dizaines de milliers.
Paramètres influençant l’injection de métal vs le moulage sous pression
Avant de choisir ce processus, il est important de connaître les facteurs affectant la qualité et le coût de la pièce. Regardons quelques paramètres courants:
Nº | Paramètres | Injection de métal (MIM) | Moulage sous pression |
1 | Densité | 98% | 100% |
2 | Résistance mécanique | Élevée | Élevée |
3 | Finition de surface | Élevée | Moyenne |
4 | Miniaturisation | Élevée | Faible |
5 | Complexité géométrique | Élevée | Moyenne |
6 | Flexibilité de conception | Élevée | Moyenne |
7 | Capacité de paroi mince | Élevée | Moyenne |
8 | Plages matérielles | Élevées | Moyennes |
9 | Productibité | Élevée | Moyenne |
10 | Faisabilité post-opération | Bon | Bon |
11 | Tolérance dimensionnelle | Élevée | Moyenne |
Avantages et inconvénients de l’injection de métal et du moulage sous pression
Comme tout processus de fabrication, le moulage sous pression et l’injection de métal ont leurs avantages et leurs limites. Prenons par exemple;
Avantages de l’injection de métal
- Vous pouvez obtenir le produit final dans des dimensions et une finition précises. Pas besoin de finition ou d’usinage supplémentaires.
- C’est un choix parfait pour plusieurs alliages
- Vous pouvez créer n’importe quelle forme, même avec une structure et une géométrie complexes
- L’option existe pour apporter des ajustements de production de manière pratique
- Cela n’a aucun impact négatif sur l’outillage. Cela signifie que vous devez dépenser moins pour vos outils.
- Vous pouvez traiter la surface du composant comme vous le souhaitez. Il offre une compatibilité avec différents traitements de surface.
Inconvénients de l’injection de métal
- Il coûte plus cher par rapport au moulage sous pression
- La durée de vie de l’outil dans ce processus est très courte. Il prend en charge des prises allant de 150 000 à 300 000.
- Il y a une possibilité que les pièces rétrécissent d’environ 30%
- La configuration initiale requiert des dépenses substantielles
Avantages du moulage sous pression
- Vous permet d’économiser plus de 30% sur les dépenses par rapport à l’injection de métal
- Le moulage sous pression vous permet de profiter d’une plus longue durée de vie de l’outil allant jusqu’à 1 million de prises
- Le moulage sous pression est entièrement automatisé. Vous n’avez pas besoin de dépenser pour les coûts de main-d’œuvre
- Prend en charge une multitude d’applications dans de multiples industries
- L’option existe pour créer des inserts ou des fixations complexes pour les produits finis
Inconvénients du moulage sous pression
- Vous pouvez rencontrer de la porosité dans le produit final complexe
- L’outil coûte généralement plus cher et nécessite d’être soumis à une température et une pression plus élevées
- Le coût de configuration pour le moulage sous pression est plus élevé
- Pas approprié pour réaliser la production sur un petit volume
Gaspillage de matière: Injection de métal vs moulage sous pression
Processus de moulage sous pression
Le gaspillage de matière indique la matière qui n’est pas utilisée ou fait référence aux déchets. Plus il y a de déchets générés, moins l’efficacité du processus est élevée.
Dans le moulage sous pression, la génération de déchets ou de rebuts est plus élevée que le gaspillage dans l’injection de métal. En ce qui concerne la consommation de matière, l’injection de métal utilise une faible quantité de matière. La principale raison d’une moins grande génération de déchets est le système automatique d’alimentation. L’injection de métal génère moins de 5% de déchets par rapport au moulage sous pression.
Conclusion
Même en comparant l’injection de métal et le moulage sous pression, il est clair qu’ils jouent un rôle important dans la fabrication des pièces en métal.
À partir des informations ci-dessus, il est évident que le coût, le processus de fabrication et la qualité de la pièce varient en fonction du processus.
Plus de ressources:
Moulage sous pression – Source : Wikipédia
Processus de moulage sous pression – Source : Dynacast
Moulage de pièces métalliques – Source : Custom Part
Injection de métal – Source : Wikipédia
MIM – Source : Custom Part
Processus MIM – Source : Annuaire IQS
Fabrication de tôlerie – Source : KDM